Aerial Bucket Truck Safety: Hydraulic System Pollution
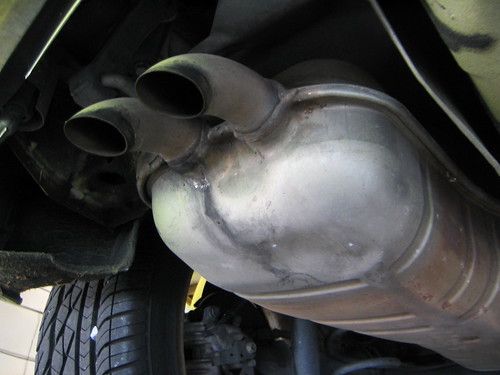
It's difficult to imagine how aerial bucket trucks are able to move their booms and lift heavy loads. Basically, this bucket truck gets its lifting capability from a powerful diesel engine. The power is converted to lift heavy loads via the hydraulic system. The amazing thing about this accomplishment is that the medium for transmitting all that power is simply a viscous liquid called hydraulic fluid.
Today, the bucket truck has progressed to become a safe piece of equipment with plenty of failsafe mechanisms to protect the employee working inside the bucket should this lifting method ever fail. One component that keeps the bucket truck safe is the integral holding valve that is built in to the cylinder. Its purpose is to hold the boom in position if a failure occurs between the cylinder and the directional valve.
Structure Vulnerable to Breakdowns
Despite these fail-safe features, the structure is still vulnerable to breakdowns. One of the most common causes is pollution. As a matter of fact, 75% of all hydraulic failures are caused by dirt inside the mechanism, and only 25% is due to pure mechanical failure.
Supposedly, the device is free from any foreign material for optimum service life; however, sometimes during production or between servicing, debris such as iron filings, sand, excess sealant, dust and chipped paint can contaminate it.
Effect of Foreign Debris
Foreign debris can contaminate different parts during production if the production area isn't clean and well ventilated. Dust particles can easily enter the orifices of the hydraulic parts and contaminate the system. The same problem can occur when it is serviced by non-specialized technicians. Bad repair practices can easily introduce foreign debris into the apparatus.
Despite their size, pollutants can easily damage different parts of the hydraulic system and compromise its safety. Small paint fragments or metal shavings can potentially block fluid inlets restricting or reducing the flow or totally blocking the movement of the fluid.
Even microscopic debris can have a detrimental effect on the hydraulic system. Specks of dust and other small solid fragments can wear out oil seals causing leaks and releasing pressure from the structure. Solid pollutants can also get in-between moving parts and restrict their movement. The added friction could also speed up the part's wear and tear resulting in the necessity of service much sooner.
Lack of Proper Servicing
Aside from foreign debris, another cause of system pollution is the lack of regular servicing. Hydraulic fluids should be changed regularly as prescribed by the truck manufacturer. Fluids will change property over time due to factors such as heat and pressure as well as the addition of shavings from the structure's moving parts during normal operation. The changes in the fluid's viscosity, as well as the accumulation of dirt, can also affect the system's performance.
Pollution inside the system can potentially reduce the lifts upward ascent capability, be the cause of a slowed response, or worse yet, totally fail during operation.
Use Manufacturer's Replacement Parts
To prevent hydraulic system pollution, it is important to purchase aerial bucket trucks with brand names from well-known and established manufacturers. Servicing should also be performed only by authorized technicians. Whenever parts replacement is required such as the hydraulic oil filter system, only use replacement parts recommended by the truck manufacturer.
Lastly, follow the truck's regular maintenance schedule. If these guidelines are followed, the breakdown of any part of an aerial bucket truck due to hydraulic system failure caused by pollution into the system should not happen!
No comments:
Post a Comment